What is a Enclosure in Electrical Panel ?
The enclosure is a just gray box which can be made of SS, MS, aluminum and thermoplastics material and the main purpose of this box to protect the inside components, instrument or device from their surrounding environment and also to protect the operator or worker there might be around the enclosure form any electrical hazard with in enclosure.
So that when we are designing any control panels we should carefully select the enclosures, check the site environment condition. Whether indoor or outdoors, electrical enclosures must weather corrosive elements such as dust, temperature, chemicals, and moisture from rain or humidity. After finalizing the enclosure for the electrical panel also select the suitable enclosure IP ratting .
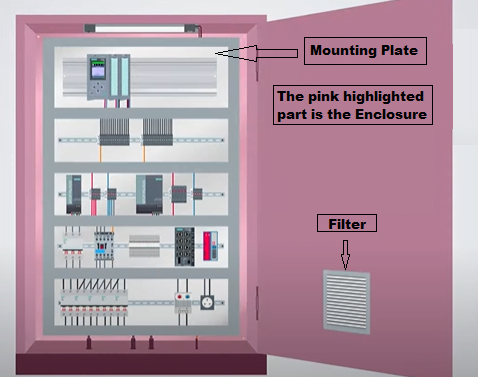
Selection of the enclosure material
So whenever we are selecting the enclosure material we should keep in mind the environmental condition of the site.
Electrical enclosures are generally made by metals such as mild steel (MS), stainless steel (SS), aluminum or plastic. mild steel (MS) cabinets can be painted or galvanized, powder coating we can use it outdoor as well as indoor. And plastic enclosures are used for indoor applications not in stringent (harsh) environments. Polycarbonate, glass-reinforced, and fiberglass enclosures are used where sturdier cabinets are required, and may additionally be gasketed to keep out dust and moisture.
So basically Main 3 Materials
1. Metal (MS, SS and Aluminum)
2. Thermoplastics
3. Fiberglass
1. Metal
Carbon steel, stainless steel and Aluminum are commonly used for electrical enclosure due to Their high durability, strongest and corrosion resistance among construction options.
Carbon steel costs less but we need to be painted (RAL 7035 color) or galvanized to resist corrosion and it is easier to modify after fabrication for installation. Carbon steel may be hot or cold rolled. Hot rolled carbon steel is used for stamping and medium forming applications. Cold rolled sheet is produced from low carbon steel and then cold reduced to a certain thickness.
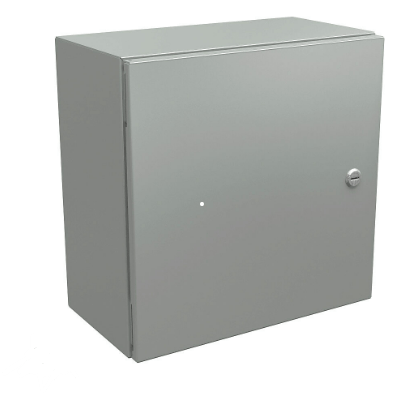
Stainless steel enclosures are suited for medical, pharma and food industry applications as they are bacterial and fungal resistant due to their non-porous quality. Stainless steel enclosures are more durable and longer-lasting, but also harder to modify later. For example, food manufacturing areas may be specified to allow wash-down cleaning.
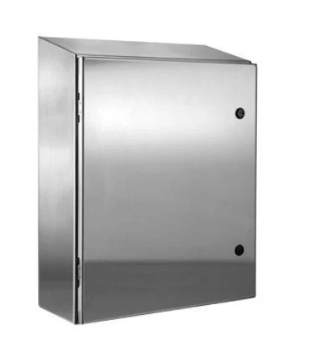
Aluminum is chosen because of its lighter weight and more durable and long lasting, but it is also difficult to modify later like SS (stainless steel), relative strength, low cost and corrosion resistance. It performs well in harsh environments and is strong, able to withstand high impact with high malleable strength.
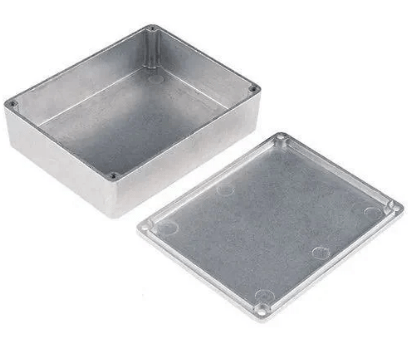
2. Thermoplastics or Polycarbonate
Polycarbonate Used for electrical enclosures Strong, highly resistant in corrosive environments and very easily modified for expansion or installation but light, non-conductive and non-magnetic.
Thermoplastic is best at insulation, so choose this material for the most temperature-sensitive electrical controls. However, thermoplastics are also much less customizable during the design and manufacturing phase, Therefore you may be limited by the base size and shape available.
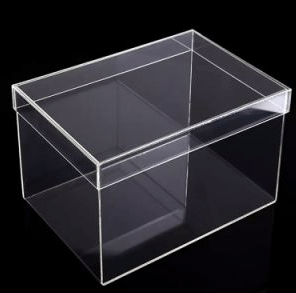
3. Fiberglass
Fiberglass enclosures resist chemicals in corrosive applications. At both ends of the spectrum, this material has both strengths and weaknesses. Fiberglass is resistant to corrosion or oxidation from corrosive elements and offers the highest chemical resistance. However, fiberglass enclosures are very hard and abrasive to equipment, making them the most difficult to shape and modify later. Fiberglass also tarnishes quickly from exposure to sunlight and heat over a long period of time, so the applications for fiberglass are very specific.
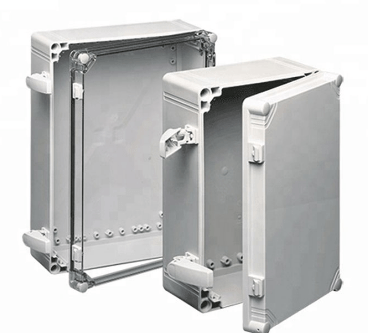
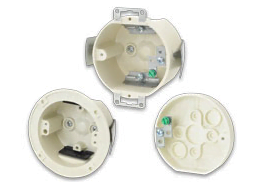
Leave a Reply